Clean rooms
Precision Polymer Engineering operates five clean rooms dedicated to the manufacture of elastomer components for the semiconductor, food/dairy, and pharmaceutical/medical industries.
- UK: Three clean rooms totalling 254 sq.m. (2734 sq.ft.) – for milling, molding and inspection operations in a Class 10,000 (ISO Class 7) environment. There is also a separate area for cleaning and packaging to Class 1,000 (ISO Class 6)
- USA: Two clean rooms totalling 454 sq.m. (4885 sq.ft) – for milling, molding, inspection, cleaning and packaging operations in a Class 1,000 (ISO Class 6) environment.
At PPE, we believe it is not enough to simply clean and package products in a clean room. Our high performance seals are also compounded, extruded, and molded in a clean room environment. This ensures maximum cleanliness and purity.
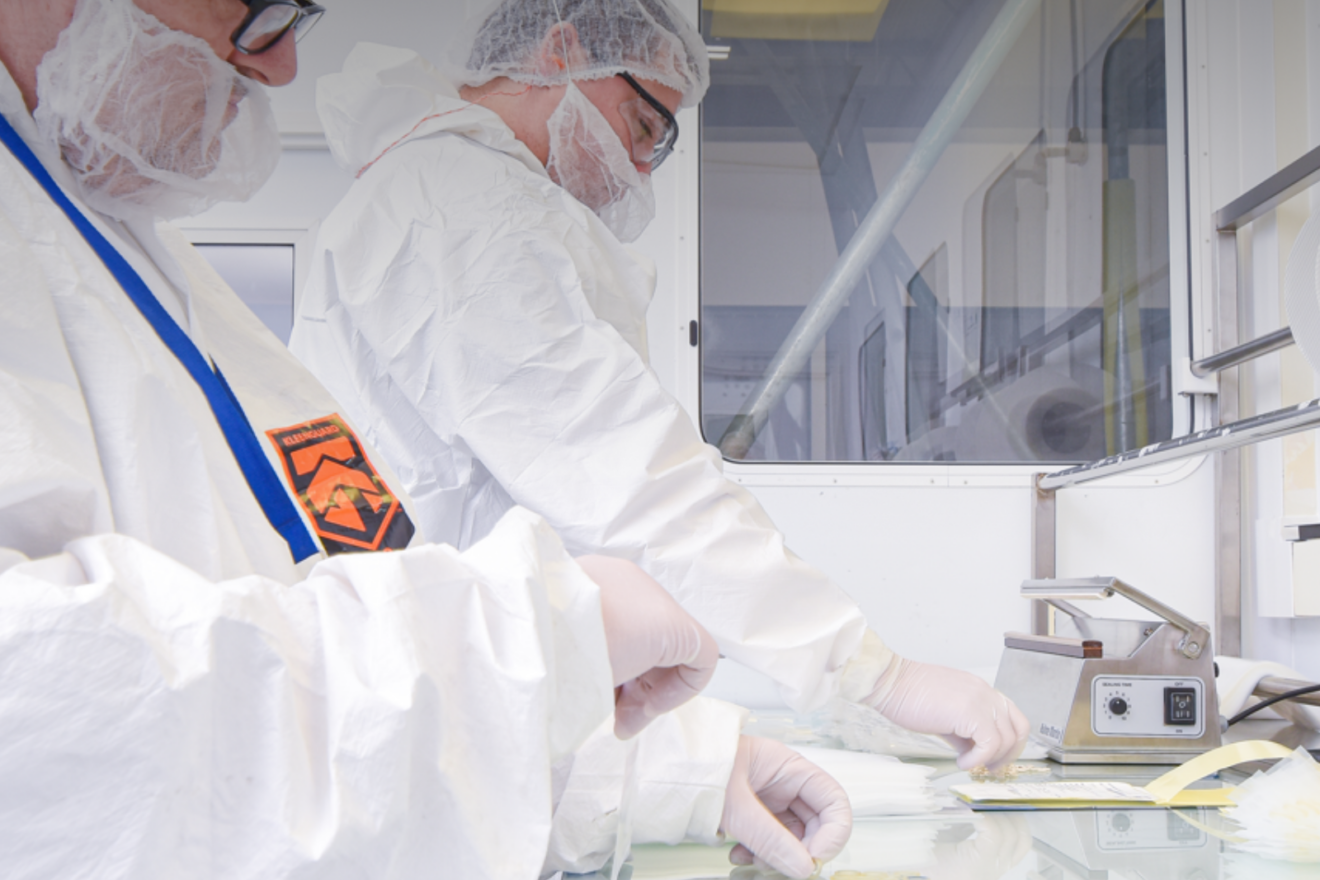
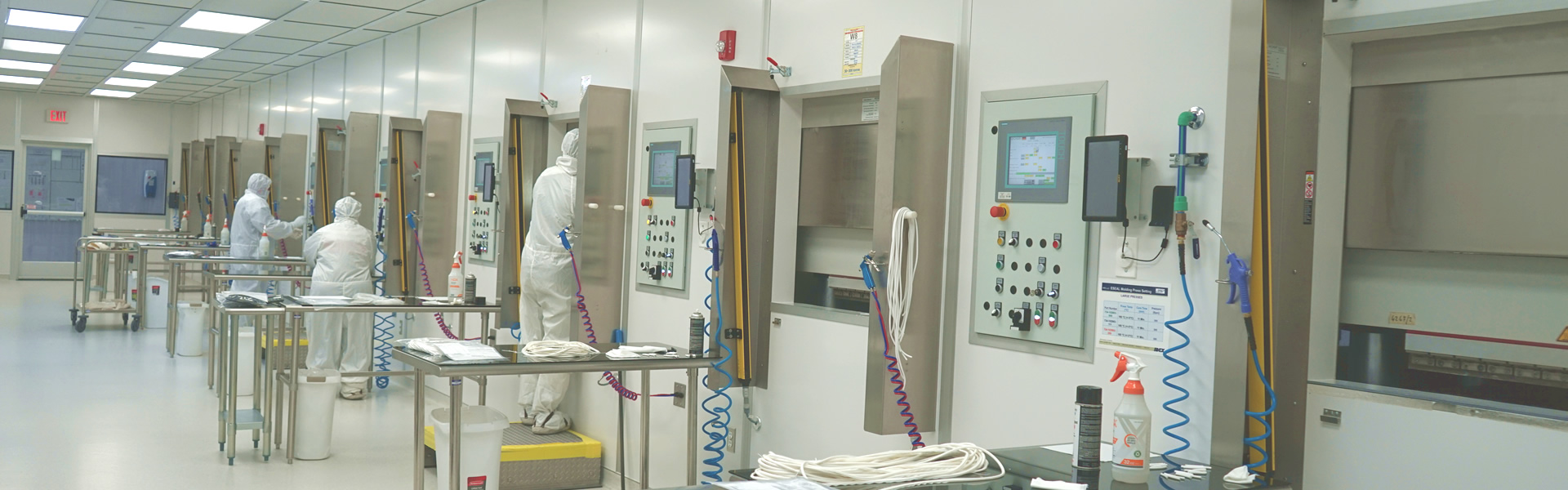
High purity elastomer sealing for critical sealing environments where purity counts
What is a clean room?
A clean room is a controlled manufacturing environment that has a low level of pollutants such as dust, airborne microbes, aerosol particles, and chemical vapors.
Environmental parameters such as temperature, humidity, and pressure are carefully controlled, with air delivered to the clean room through HEPA filters.
PPE material brands
PPE’s clean room environments in the UK and USA enable the production of the highest quality and cleanest sealing components, in high purity elastomer materials such as Perlast®, Kimura®, and Nanofluor®.

Perlast®
expand_moreThe ultimate perfluoroelastomers for sealing applications where chemical resistance and high temperature performance are critical.
Kimura®
expand_moreHigh purity, fully organic elastomers for semiconductor applications.
Nanofluor®
expand_moreA range of advanced, ultra-pure elastomers utilizing a nano-filler system
Products
Below is a selection of the most common sealing products manufactured in our clean room environments.